Do or dye: New life for 500-year-old craft
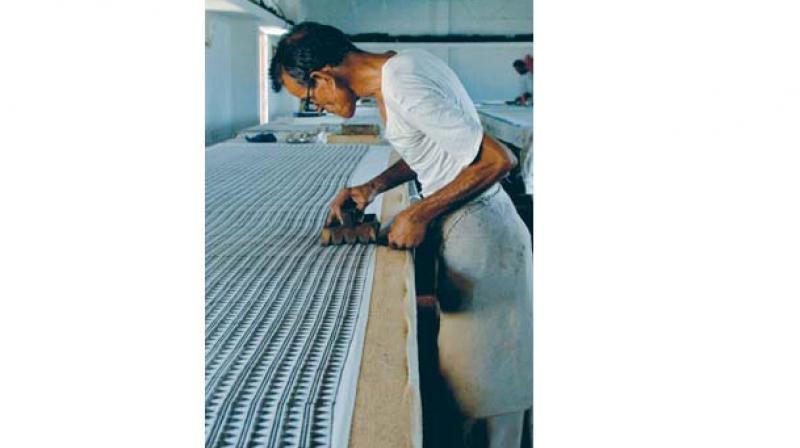
Dabu, the five hundred year old craft, began with a tale. That tradition continues, and continues today, through the simple, albeit universal motifs and the multitude of stories. Legend has it that a Rangrej (dyer), did not notice the mud from the riverbank clinging to his dhoti, as he made his way back from his daily trip. The next day, a heap of clothing, the dhoti included, were put in to a vat of indigo. It was only when he put them out to dry that the Rangrej found, to his astonishment, that the spots where the mud had clung to the dhoti had not been coloured by the indigo. He began experimenting, smearing mud, now in patterns, over pieces of cloth, which he then proceded to dye.
Whether or not the story is true, the hand-printing tradition, or Dabu, as it is known in Rajasthan where it is practiced, continues to be rooted in the same traditions. "We collect mud from the riverbank, which we mix with lime and natural gum," says Alka Sharma, the founder of Aavaran. This mixture of calcium hydroxide, pounded wheat chaff and gum are used to make the mud-resist.
"We use resin from the babul seed, which works as a binding agent," Alka explains. This is then mixed with mud, which has been soaked in water overnight and used to make a sticky paste. Wooden blocks etched with patterns are dipped into the paste and hand-pressed on the fabric.
In 2009, Alka Sharma, who had married into a family in Udaipur, founded a self-help group to support artisans in Akola, near Udaipur. A graduate of the Indian Institute of Crafts and Design, who specialised in textile studies, Alka noticed artisans struggling to make a living and their centuries-old craft slowly dying out.
"We have retained the traditional process but brought in new motifs and contemporised designs so they appeal to a larger audience," says Alka. "Every collection tells a story - we used to do one a year when we started but now there are several."
The Dabu prints make their way on to clothes, furnishings and accessories, all of which have been developed by the in-house design team made of 100 designers. Themes are conceptualised, discussed and then executed by the artisans. "We did a Krishna theme- that was our first. There was also one on birds - the themes are always local, taken from our surroundings. The motifs on their own are simple, so they appeal to everybody."
The actual process happens from scratch, with the artisans collecting mud, preparing the mud-resist and printing the textiles. "We have also trained our women in finer aspects of stitching and cutting," says Alka. "This has become a source of livelihood for these people. When I arrived here, only the handful who were employed by large chains could make ends meet. The rest had very little incentive to keep the craft alive."
They use natural dyes like indigo and turmeric and Alka says this fabric is actually good for you! "It contains natural ingredients, which have beneficial properties for the skin." About 50 kilos of Dabu are prepared everyday to prepare about six meters of a light-coloured fabric, Lep, which has been created by Aavaran.