Kerala: Building material prices wayward
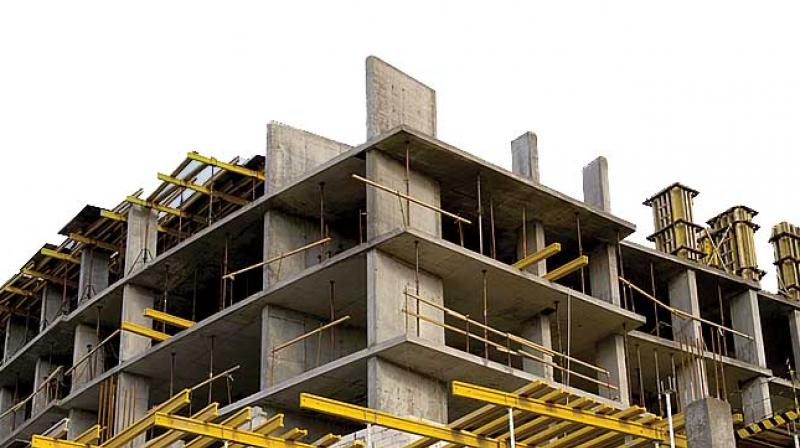
KOCHI: The building construction industry, one of the main catalysts of the Kerala economy, under stress due to the crash in the price of natural rubber and the loss of jobs by many employed in Gulf countries has also been handicapped by the volatility in the price of inputs used by the industry. The industry does not have any control over the price of cement, steel and river sand, the three major ingredients used in the construction sector. Individual home builders are also not immune to the vagaries of the price. “It is difficult to understand that the price of the commodity differs in the same city”, say aggrieved consumers.
It is well known that the price of cement, river sand and steel is higher in Kerala compared with Tamil Nadu. One cubic feet of river sand costs Rs 55 in Tamil Nadu but it goes up to Rs 80 in Kerala, says SL. Aji, a government employee based in Neyyatinkara. “The price of cement costing Rs 365 per bag in Tamil Nadu will cost me '400. The calculations of someone depending on bank loans for house construction is completely offset by fluctuations in price”, he said. Johnson Varghese, a Kochi-based contractor, feels that fluctuations in raw material prices in the same locality affect contractors and consumers. “The price of cement and steel is lesser in the city and higher in rural areas”, he said.
Though the dealers’ association had fixed a uniform price, individual shop owners sold raw materials at different rates, Mr. Varghese said. But, shops with less business volume in rural areas are forced to sell materials for lesser rates. Similar is the pricing of steel, he added. The price of raw materials for building construction varies in towns and municipal areas in Kozhikode. A customer buying a few bags of branded cement would be charged Rs 425 per bag including loading/unloading charge and transportation. For a builder, the cost would come down to Rs 415 as he took the material directly from the company. If the required quantity was more than 50 bags, the price would again slump to Rs 405, said a person connected with the sector.
Although bulk buyers enjoy such discounts, retail buyers are not so fortunate. The price would differ in the range of Rs 50 within short distances of 20 km. For instance, a local brand costing Rs 385 in Kozhikode would be Rs 400 in Koyilandy. “The advantage of selecting good brands is that the company sends its representatives to the building site in case of a problem. They offer a scientific solution to plug the problem,” says Kala C.P, Technical Manager at Forms Constructions, Kozhikode. She added that top soil was another raw material which suffered from price fluctuation. “After rains, the price would shoot up and it is a Herculean task to get soil of good quality,” she says.
K. Sadanandan, who recently constructed a house in Ulliyeri on the outskirts of Kozhikode, called for urgent government intervention in the sector. “Anarchy is the norm here. Price, quality and delivery are according to the whims of the traders,” he fumed. Purushan Eloor, building contractor based in Kochi, however said that government intervention was unlikely to bring any major changes. The price of raw materials varying in different places in the same locality was not a big problem for contractors or builders, he said. Builders could get cement at its original net price, if they were buying in bulk, he added. The higher price of Rs 10 or '20 per bag for cement is often the dealers’ margin.We also have to take into account transportation cost if the construction site is in remote areas, he said. “Though there is not much exploitation in the pricing of raw materials, the fluctuation in the market price, is having a negative impact on small and medium scale builders”, he said.
Worst-hit government opts for silence on price swing
The fluctuation in the prices of raw materials for construction, affects the government most as it is the biggest infrastructural developer. Ironically, the state government still does nothing to control prices of raw materials, say builders. A few years ago, builders used to directly get cement from companies. However, the dealer lobby raised a red flag and stopped this system bringing the pricing under their control. Today a packet of cement that costs Rs 350 can be sold at Rs 390 or Rs 420 depending on the lobby's whims. The price of granite stones and sand are very unpredictable as a quarry ban can lead to spiralling of prices locally. For instance, the shutting down of Mookunnimala quarry had made granite stones very expensive in the capital.
“A builder who is contract-bound to sell a house at specific rates will be in trouble. Also, the price of steel soars during summers as its production is dependent on the availability of electricity,” said N Reghuchandran Nair, Vice President of CREDAI. In addition, the quality of government work gets affected because it awards the tender to the one who quotes the lowest. When prices shoot up, the contractor demands a rate hike which is mostly not accepted. Then the quality is compromised and arbitration or a vigilance inquiry begins. “The government needs to declare a ceiling rate for cement and ensure companies and dealers adhere to it. This works in many states and it should work here,” he said.
Builders in the state are finding it harder to survive price fluctuations as several residential units remain unsold, mostly in pockets like Kakkanad in Kochi. The Competition Commission of India had recently slapped a fine for thousands of crores on major cement companies for cartelisation. Although the government established the Real Estate Regulatory Authority (RERA), builders are angry with it as it gives them no assurance of a level playing field. “If the government wants to jail erring builders, obviously consumers won’t ever get delivery of the building. So there has to be a policy to give these builders a level playing field. Then they should be pressurised to deliver on time adhering to all legalities,” Mr Nair said.